In logistics, manufacturing, and other industries where accurate weight measurement is vital, choosing the right weighbridge solution can be daunting. With numerous hardware and software solutions options, it's essential to understand the differences and make an informed decision based on your specific needs. This article compares weighbridge software and hardware solutions to help you choose the right solution for your requirements.
What is a Weighbridge?
A weighbridge is an extensive weighing system designed to measure the weight of vehicles and their loads accurately. These systems are commonly used in various industries, including logistics, construction, waste management, and agriculture, to ensure accurate weight measurements for inventory control, legal compliance, and efficient transportation.
Hardware Weighbridges
There are two main types of hardware weighbridges: mechanical and electronic.
Mechanical Weighbridges
These traditional weighbridges consist of a mechanical platform and lever system with counterweights to determine the weight of a vehicle. While mechanical weighbridges are known for their durability and simplicity, they may require more maintenance and can be less accurate than their electronic counterparts.
Electronic Weighbridges
Electronic weighbridges utilize advanced technology, including load cells and digital indicators, to measure vehicle weight accurately. These systems are generally more accurate, require less maintenance, and can be easily integrated with data management and analysis software solutions.
Software Weighbridges
In addition to hardware weighbridges, there are also software solutions available that can help streamline your weighing operations. These solutions come in two main categories:
Standalone Software Solutions
These are independent software applications designed specifically for weighbridge management. They can handle ticketing, reporting, and data analysis tasks ticketing, reporting, and data analysis, improving efficiency and reducing human error.
Integrated Software Solutions
Integrated software solutions can connect with your existing business management software, such as ERP or inventory management systems, to seamlessly integrate your weighbridge and other business operations.
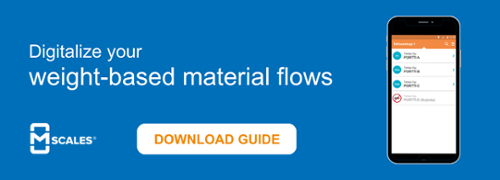
Factors to Consider when Choosing a Weighbridge Solution
When comparing weighbridge hardware and software solutions, consider the following factors:
Accuracy
Accuracy is critical for any weighing system. Choose a solution that provides the highest level of accuracy within your budget and requirements.
Durability and Maintenance
Consider the durability of the system and the required maintenance, as this can impact your weighbridge solution's long-term cost and reliability.
Ease of Use
Choose a user-friendly solution that minimises the learning curve for operators and reduces the potential for errors.
Integration with Existing Systems
If you have existing software systems, consider a solution that can integrate seamlessly with these systems to streamline your operations further.
Cost
Compare the initial investment and ongoing costs, such as maintenance and software updates, to determine the most cost-effective solution for your needs.
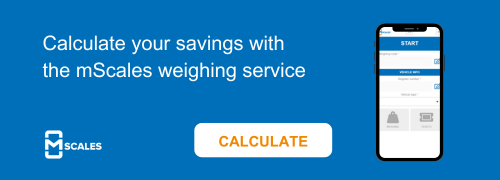
Software vs Hardware: Pros and Cons
To make a well-informed decision, weighing the pros and cons of hardware and software weighbridge solutions is essential.
Hardware Weighbridges: Pros and Cons
Pros:
- Often more durable and robust, making them suitable for harsh environments.
- Can be used independently without the need for additional software.
Cons:
- May require more frequent maintenance, especially for mechanical weighbridges.
- Less flexible in terms of data management and integration with other systems.
Software Weighbridges: Pros and Cons
Pros:
- Offers better data management, analysis, and reporting capabilities.
- Can integrate with existing business management systems for a seamless workflow.
Cons:
- May require a higher initial investment, especially for integrated solutions.
- May have a steeper learning curve for operators.
When choosing the right weighbridge solution for your needs, it's crucial to consider factors such as accuracy, durability, ease of use, integration with existing systems, and cost. While hardware weighbridges offer durability and independence, software solutions provide improved data management and integration capabilities. By carefully weighing the pros and cons of each option and considering your specific requirements, you can make the best decision for your business.

FAQs
What is the difference between mechanical and electronic weighbridges?
Mechanical weighbridges use an automated platform and lever system with counterweights, while electronic weighbridges use load cells and digital indicators for more accurate weight measurements.
Do I need a software solution if I have a hardware weighbridge?
While not strictly necessary, a software solution can significantly improve data management, reporting, and integration with other business systems, making it a valuable addition to your weighbridge setup.
Can a software weighbridge solution work with my existing business management software?
Yes, integrated software solutions are designed to connect with existing business management software, such as ERP or inventory management systems, providing seamless integration between your weighbridge and other business operations.
What factors should I consider when choosing a weighbridge solution?
Consider factors such as accuracy, durability, ease of use, integration with existing systems, and cost when choosing a weighbridge solution.
How do I determine the most cost-effective weighbridge solution for my needs?
Compare the initial investment and ongoing costs, such as maintenance and software updates, to determine the most cost-effective solution for your needs.
Let's discover together the benefits for your business!