When weighing results affect product quality or billing, it’s essential to keep your scale calibration and verification up to date. These are key parts of maintaining a weighing system, and they directly impact the reliability efficiency and legal compliance of your business operations.
Even the most advanced industrial scale won’t stay accurate forever. Over time, mechanical wear, environmental factors and daily use can affect performance. That’s why regular checks and adjustments are needed to ensure measurement accuracy. In this article, we’ll explain what weighing system calibration and weighing system verification mean, why they matter, and how they support your business in daily operations.
Verification vs. Calibration – What’s the Difference?
Weighing system verification and calibration may seem similar at first, as both involve comparing the scale’s readings to known reference weights. In reality, they are two different procedures, each serving its own important role in maintaining a reliable weighing system.
Verification is an official process required by regulatory authorities to ensure that a scale meets the legal standards for accuracy and use. It may include adjustments if needed, but its primary purpose is to confirm that the device complies with regulations and is approved for official use. Any scale used in commercial transactions must be verified by law.
Calibration of weighing equipment, on the other hand, is a voluntary process that evaluates how much a scale’s readings deviate from true values. It is commonly used in production environments where precise ingredient dosing and consistent quality are essential. Regular weighing system calibration helps maintain process stability and ensures that measurement results are repeatable, traceable and trustworthy.

What Verification Ensures – And When It’s Legally Required
The more important weighing data is to your business, the more critical it is that the scale’s results can be trusted. Weighing system verification is required whenever weight data is used for commercial or official purposes, such as:
- pricing products or calculating weight-based invoices
- verifying delivery and purchase quantities
- reporting to authorities, such as for waste or emissions data
- customs and tax documentation
- tracking material flows in regulated industries
But verification is more than just a legal obligation. It’s a documented confirmation that your scale performs as it should, the conformity of the scale is valid and that its results can be used with confidence.
A verified weighing system builds trust across the board – between customers, suppliers, subcontractors and regulatory bodies. Reliable measurement supports transparency and fairness and helps protect your company’s professional reputation.
Time for verification? Check out Tamtron’s verification services.
Why Calibration of Weighing Equipment Matters
Accurate measurement is a key part of reliable and consistent production. When weight data is used to control processes, dose raw materials or ensure uniform product quality, calibration becomes essential. Without regular calibration, a scale may slowly drift out of tolerance — and even small errors can turn into significant costs over time.
Weighing system calibration is especially important when measurement data is used for:
- dosing raw materials or following precise recipes
- internal production monitoring and quality assurance
- reducing material waste and improving process efficiency
- maintaining reporting accuracy
- ensuring consistency across multiple weighing points
Regular calibration helps ensure that measurement results remain repeatable, reliable and up to date. It allows deviations to be detected early — before they affect production, customer deliveries or financial performance.
Need calibration support? Explore Tamtron’s calibration services.
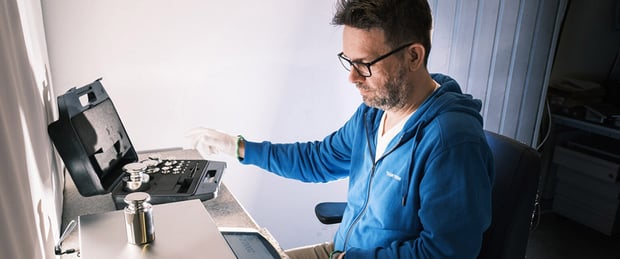
Signs Your Weighing System Might Need Calibration or Verification
In most cases, a scale stays accurate when calibration and verification are done regularly. Scale owners are typically only responsible for making sure these checks are done on time — often with the help of a service agreement or reminders from a provider.
Still, there may be situations where accuracy becomes uncertain. Certain practical signs may indicate it’s time to have the scale inspected:
- The scale does not return to zero after weighing
- Results differ from other systems or expected values
- A customer questions the weight data or invoice
- The device shows error messages or behaves unusually
- A long time has passed since the last calibration check or regular verification is approaching – Scales must be verified periodically, with intervals varying by country.
If any of these issues occur, it’s worth scheduling a check-up to avoid bigger problems later. Timely weighing system calibration or verification ensures your measurements remain reliable and your daily work flows smoothly.

A Reliable Weighing System Supports Your Entire Business
When a weighing system runs smoothly, it fades into the background — becoming a natural part of daily operations. There’s no need to question the results or double-check the data. That’s when it does its job best: supporting decisions, keeping processes moving, and building trust across the supply chain.
A well-maintained weighing system:
- supports consistent product quality
- prevents errors and customer complaints
- speeds up deliveries and receiving
- makes billing clear and accurate
- simplifies reporting and data-driven decision-making
When weighing data flows seamlessly from the scale into reporting, invoicing and other business systems, weighing becomes a smart part of the whole. A modern weighing system software integrates directly with your other tools, making data handling smooth and effortless.
Read more:
5 Advantages of using cloud-based weighbridge software
Understanding Weighbridge Software: Features, benefits & uses
Want to make sure your weighing system truly supports your business? Book a meeting to see how mScales can help streamline your weighing process: