Weight-based material flow management is critical in various industries, including manufacturing, logistics, and warehousing. Properly managing the flow of materials based on their weight can significantly impact operational efficiency and productivity. However, this process comes with its own set of challenges that can hinder smooth operations. In this blog post, we will explore the common challenges faced in weight-based material flow management and discuss potential solutions to overcome them.
What
Challenge 1: Inaccurate Weighing
Accurate weighing is crucial in weight-based material flow management. Inaccurate weighing can lead to errors in material inventory, production planning, and cost calculations. It can also result in non-compliance with regulatory requirements, leading to fines and penalties. Several factors can contribute to inaccurate weighing, such as measurement equipment malfunction, human error, and environmental factors.
Solution: Investing in high-quality weighing equipment, such as precision scales or load cells, can significantly reduce the risk of inaccurate weighing. Regular calibration and maintenance of weighing equipment are also essential to ensure accuracy. Implementing automated weighing systems can minimise human error and provide real-time data for better decision-making. Additionally, training employees on proper weighing techniques and conducting regular audits can help identify and rectify any inaccuracies in the weighing process.
Challenge 2: Complex Material Flow
Material flow in weight-based management can be complex, especially in industries that handle multiple materials simultaneously or deal with large materials. Managing the flow of materials based on their weight while also considering factors such as material type, destination, and priority, can be challenging and time-consuming. Inefficient material flow can result in bottlenecks, delays, and increased costs.
Solution: A well-designed material flow plan is crucial for efficient weight-based material flow management. Analysing historical data, conducting process mapping, and using simulation tools can help identify potential bottlenecks and optimise material flow paths. Utilising automation and technology, such as conveyor systems and automated guided vehicles (AGVs), can streamline material flow and reduce human error. Implementing real-time monitoring and tracking systems can also provide visibility into material movement, allowing for proactive decision-making and issue resolution.
Challenge 3: Compliance with Regulations
Industries that handle materials based on their weight are often subject to regulatory requirements, such as safety, environmental, and trade regulations. Compliance with these regulations can be challenging, as they vary by region, industry, or material type. Non-compliance can result in fines, penalties, and damage to reputation.
Solution: Staying updated with the latest regulations and ensuring compliance is essential for effective weight-based material flow management. Collaborating with legal and compliance teams, conducting regular audits, and implementing standard operating procedures (SOPs) can help ensure regulation compliance. Utilising software solutions that provide compliance tracking and reporting can also streamline the process and reduce the risk of non-compliance.
Challenge 4: Data Management and Analysis
Weight-based material flow management generates significant data, including weight measurements, material type, destination, and time stamps. Managing and analysing this data can be overwhelming, especially if done manually. However, data-driven insights are crucial for identifying trends, optimising processes, and making informed decisions.
Solution: Implementing a robust data management system is essential for effective weight-based material flow management. Utilising digital solutions, such as data analytics software and warehouse management systems (WMS), can help automate data collection, analysis, and reporting. Creating dashboards and visualisations can provide real-time insights into material flow performance, enabling data-driven decision-making. Collaborating with data scientists or hiring dedicated data analysts can also help harness the full potential of data for process optimisation.
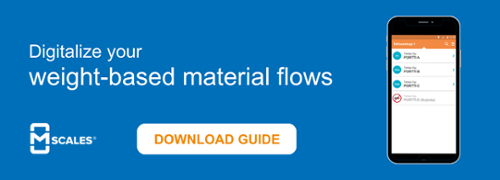
Conclusion: In conclusion, weight-based material tracking is a powerful strategy to optimise supply chain operations. Accurate weight measurement, real-time data collection, integration with supply chain systems, waste reduction, and compliance with industry regulations are key principles of effective weight-based material tracking. Implementing robust weight-based material tracking systems can improve operational efficiency, reduce costs, minimise waste, enhance sustainability, and comply with industry regulations. By harnessing the power of weight-based material flows, businesses can gain a competitive edge in the market and achieve supply chain excellence

Case Studies and success stories of weight-based material flow implementation:
Customer case: Nordkalk is a pioneer with a digital weighing solution.
Introduction to weight-based material flows
Let´s discover together the benefits to your business!